Tiempo estimado de lectura: 4:10 min
Eficiencia y Ecología juntas con el programa KAESER CARBÓN CERO
Los compresores de aire se utilizan generalmente para aplicaciones que exigen un óptimo rendimiento y la máxima potencia en todo momento. Los gastos derivados de los sistemas de aire comprimido pueden representar una parte significativa de los gastos generales de la empresa. Por lo tanto, es fundamental que los sistemas que utilizan aire comprimido funcionen de la forma más eficiente posible, con el menor consumo de energía posible.
En términos de relación general potencia-generación, el rendimiento de un compresor a tornillos rotativo lubricado suele ser el siguiente:
1 kW de potencia por cada 0,18 m3/min de aire comprimido a 8 bar(g).
Por parte del tratamiento del aire comprimido por el sistema de refrigeración no cíclico de gas caliente (sistema HBPR= Hot by pass regulator) enfriado por aire podría ser:
1 kW por cada 9 m3/min de aire comprimido a 8 bar(g) a una temperatura ambiente de 20°C y 30% de humedad relativa.
Secador de aire comprimido por refrigeración no cíclico por gas caliente
Cuando el aire comprimido llega a las bocas de consumo, se convierte en una forma de energía que se utiliza para accionar equipos neumáticos.
Un ejemplo de este proceso es la operatividad de un motor neumático, que podría utilizarse para accionar una mezcladora neumática de pintura, donde podría ser la relación aire/potencia:
1,6 m3/min de aire comprimido consumido por 1 kW de potencia en el eje del motor.
Si los referimos al propio compresor de aire, esto equivaldría a 8,8 kW de potencia que consume durante todo el proceso.
En resumen, exceptuando los factores de fugas y diferenciales de presión, del sistema completo, la eficiencia energética razonable durante el proceso de conversión es inferior al 10%. (Ratio promedio aproximado de 8 a 1).
¿Qué ocurre con la energía consumida?
Los usuarios del aire comprimido se sorprenden por la escasa conversión de energía y se preguntan qué ocurre realmente con el resto de la energía. Sin embargo, como resulta evidente en cualquier sala de compresores, el calor es la principal salida de una unidad de compresión. Por lo tanto, la mayor parte de la energía que entra en el compresor se convierte en calor.
La relación equivalente se explica de la siguiente manera:
1 CV = 0,746 kW= 2.545 BTU/h = 1,0 kVA
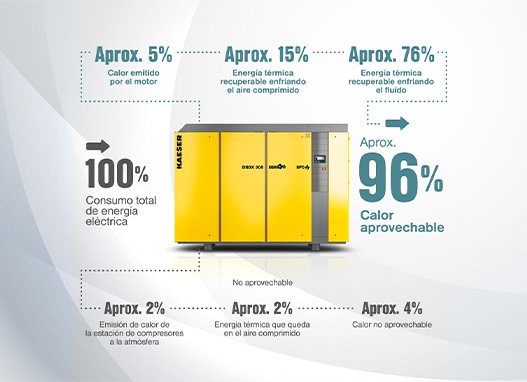
Secador de aire comprimido por refrigeración no cíclico por gas caliente
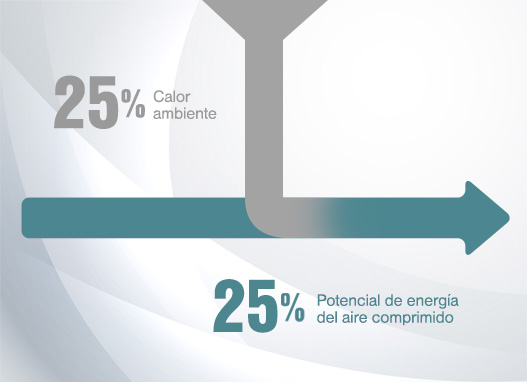
Calor potencial ambiental adicional al aire comprimido
De tal manera el 96% de la energía eléctrica se convierte en calor y se pierde a través de pérdidas por radiación. Este calor puede ser recuperado y ser utilizado para diferentes aplicaciones para el calentamiento de aire o agua. Según los estudios realizados en las plantas de prensado, sólo la mitad de todo el aire comprimido que producen las máquinas se destina realmente al uso previsto. La otra mitad consumida es debida a:
• Entre 1/4 y 1/3 del aire comprimido termina en fugas del sistema antes de llegar a las bocas de consumo.
• Aproximadamente 1/8 del aire comprimido se desperdicia en las bocas de consumo debido a la sobrepresión utilizada, que puede superar la cantidad necesaria para la aplicación.
• Las cantidades restantes de aire comprimido que aparentemente se desperdician lo hacen por una razón; el aire se utiliza para funciones operativas internas del propio sistema, el estado en vacío de los compresores cuando no existe demanda. Un ejemplo de uso internalizado sería la función de los drenadores de condensado, que consumen ciertas cantidades de aire comprimido para la extracción del condensado. Además, el aire puede consumirse cuando el compresor se deja al vacío sin carga entre los consumos operativos.
Podemos observar el grafico sobre la utilización del aire comprimido en el sistema:
Utilización del aire comprimido
De acuerdo a estudios realizados por los fabricantes de compresores, casi dos tercios (65%) de los sistemas industriales utilizan un perfil de carga 24/7, en el que el aire se comprime a altas demandas durante turnos de 16 horas los días laborables, pero de menor demanda durante la noche y los fines de semana.
Como ejemplo, el resultado del análisis de la demanda anual de aire comprimido dio el resultado del siguiente estudio de consumo:
• Días laborables/ turno diurno: dos compresores | 4.100 h | 28 m3/min | 8 bar(g) | 202,3 kW | 16,2 kW secador frigorífico = 895.850 kW-h
• Días laborables/ turno noche: un compresor | 2.000 h | 15 m3/min | 8,5 bar(g)| 113,0 kW | 16,2 kW secador frigorifico = 258.400 kW-h
• Fines de semana/parada de planta: un compresor | 2.660 h | 10 m3/min | 8,5 bar(g)| 95,8 kW | 16,2 kW de secado = 297.920 kW-h
El resultado del consumo eléctrico promedio anual a 8.760 horas es de un caudal de 19,8 m3/min y un consumo de potencia de 165,8 kW. A un costo de 0,10 USD por kWh, este sistema gastó anualmente USD 145.220 en facturación eléctrica.
El resultado de la auditoría resultó que sólo la mitad del aire comprimido se utiliza para la producción, el resto consume dinero por suministrar potencia al sistema.
Para mas información sobre las auditorías por favor contacte al siguiente correo electrónico: info.argentina@kaeser.com
CONSULTAR AHORA
Fotos fuente: Kaeser Kompressoren