¡Y con sopladores KAESER!
¿Qué tiene que ver la nata con el aire comprimido? Se lo explicamos con la historia de éxito de la central lechera bávara BMI (Bayerische Milchindustrie eG) de Zapfendorf. El tema es el tratamiento de las aguas residuales industriales de una central lechera con el objetivo de conseguir agua limpia.
Agua limpia: El objetivo se cumplió gracias a máquinas que son al mismo tiempo fáciles de manejar y fiables y que están preparadas para el futuro. Además, era importante el criterio de los costes, que debían ser lo más bajos posible. La materialización del proyecto fue una estación de soplantes de tornillo.
Central lechera Bayerische Milchindustrie de Zapfendorf
La BMI es una cooperativa lechera con larga tradición y experiencia internacional. Su fábrica más grande se encuentra actualmente en Zapfendorf, en el norte de Baviera. Junto con los productos estándar, como son la leche desnatada o el suero dulce en polvo, la empresa manufactura cada vez más productos especiales. Por ejemplo, producen concentrados proteínicos de primera calidad sirviéndose de los métodos de ultrafiltración más modernos. Estos productos ganan cada vez más importancia en la industria de la alimentación, la dietética, la alimentación infantil y las medicinas naturales. La fabricación de lactosa y de leche con grasa añadida y otros productos lácteos, así como sueros parcialmente azucarados y concentrados de poliamina completan el programa de productos. En la central de Zapfendorf se encuentra también la moderna fábrica de productos frescos, como mantequilla, nata, queso fresco y lácteos acidificados.
Alta eficiencia energética gracias a las soplantes de tornillo
Debido al aumento de la demanda y, en consecuencia, de la producción, en el año 2014 comenzaron a planificar un sistema de mayores dimensiones para purificar el agua resultante de sus procesos. Cuatro reactores Batch secuenciales debían eliminar biológicamente los nutrientes contenidos del agua residual que se fuese acumulando en distintas cantidades. Cuatro soplantes suministrarían el aire necesario para los microorganismos implicados en este proceso.
Para mantener los costes de servicio del sistema de tratamiento de aguas lo más bajos posible, se instalarían soplantes de tornillo, nuevas por entonces en el mercado, en lugar de las soplantes de émbolo usadas hasta aquel momento, ya que el proceso de activación consume mucha energía. Las soplantes de tornillo son básicamente compresores de tornillo optimizados para la baja presión y que funcionan sin aceite, con una eficiencia mucho mejor a partir de diferencias de presión de 400 mbar. Sus rotores de tornillo con PERFIL SIGMA les permiten alcanzar un rendimiento mayor. La BMI trabaja con diferencias de presión entre 600 y 800 mbar y las soplantes están en marcha durante muchas horas, como suele pasar siempre en la tecnología hidráulica. El resultado es un ahorro de energía y costes más que notable.
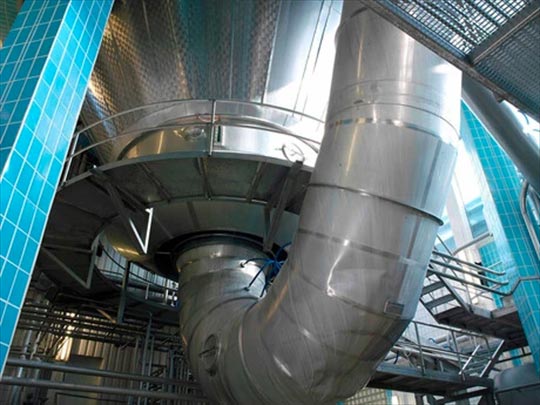
Los primeros bocetos de planificación de la BMI preveían soplantes de tornillo de primera generación, es decir, máquinas convencionales incompletas: casi siempre componentes mecánicos sueltos para cuyo montaje posterior se contrata a empresas externas que confeccionan, entre otras cosas, los armarios de distribución para completar el sistema eléctrico que les permita funcionar. Pero como por aquel entonces empezaban a abrirse paso en el mercado las soplantes de tornillo de nueva generación, esto es, máquinas completas con unidad de control y de potencia, el cliente se fijó inmediatamente en ellas.
Preparadas para la Industrie 4.0
En realiadad, el hecho de que estas máquinas fuesen «completas» fue el factor decisivo al elegirlas. En el caso de la BMI de Zapfendorf se trata de soplantes de tornillo del modelo FBS-M-SFC con convertidor de frecuencia integrado y con controlador inteligente SIGMA CONTROL 2. Gracias a este controlador, la máquina se conecta por Profibus al puesto de mando, desde donde se pueden consultar todos sus datos de servicio y estado. Desde el puesto de mando se introducen las velocidades de las soplantes, y con ellas, el flujo volumétrico que han de generar. Las soplantes se controlan en remoto por medio del sistema bus.
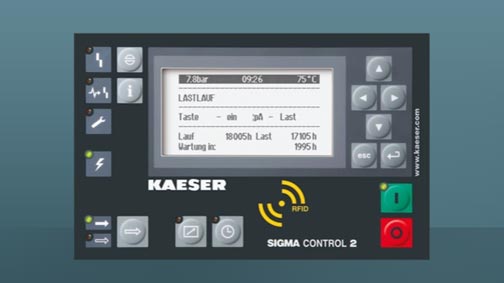
SIGMA CONTROL 2
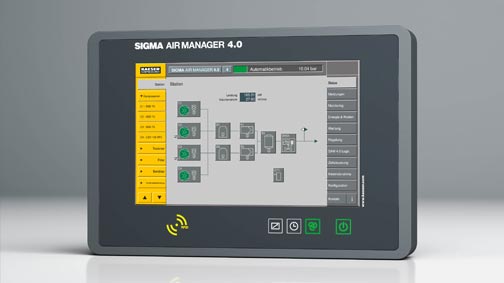
Industrie 4.0
Gracias a su sistema de control y a su estructura completa, estas máquinas son adecuadas para todas las aplicaciones de la Industrie 4.0 o Agua 4.0. Esta profunda transformación de la producción industrial se conoce también como la 4ª Revolución Industrial y exige como base la posibilidad de comunicación total entre las máquinas, así como entre ellas y el sistema de mando superior, en el marco de una integración en redes y digitalización más avanzadas. El objetivo es conseguir un control más flexible de la máquina y un diagnóstico en tiempo real de sus datos de servicio y estado (el llamado «Condition Monitoring») para garantizar un servicio óptimo y poder realizar un mantenimiento predictivo (Predictive Maintenance). Esto significa que es posible leer en una dirección una gran cantidad de datos sobre el estado de servicio y de mantenimiento de la soplante, y que la propia soplante puede ser controlada en remoto en la otra dirección – idealmente solo por medio de un cable, un cable bus de datos.
“
Hemos quedado convencidos por la oferta de KAESER: Alta eficiencia con valores de garantía constantes, una máquina complesta con sistema eléctrico, CF integrado, motores IE4, sistema de sensores y conexión al sistema superior de mando por Profibus.
“
Björn Wittmann, de la central lechera Bayerische Milchindustrie eG de Zapfendorf
Un paquete completo garantiza la seguridad de servicio
Es posible leer en tiempo real como valores analógicos, por ejemplo: La presión de aspiración, la final y la diferecial, la temperatura del aceite y del interior de las capotas silenciadoras, la caída de presión del filtro de aspiración, la velocidad en el caso de haber un convertidor de frecuencia, la potencia absorida por el convertidor y la tensión del circuito intermedio. Se monitorizan la temperatura de los motores y su potencia absorbida, el nivel de aceite, las temperaturas de las platinas del sistema eléctrico y muchas cosas más.
Cada uno de estos valores tiene asignado un umbral para generar un aviso de advertencia o de avería y que puede implementarse también en el sistema de control de preocesos por medio de un protocolo bus, permitiendo así una monitorziación más cómoda y sencilla. A esto debemos añadir los contadores de horas de servicio de la máquina y de sus componentes, como son el bloque compresor, el motor, el controlador, la unidad de potencia, componentes de mantenimiento, etc. Para los componentes de mantenimiento, como el filtro de aspiración, el de aceite, las correas trapezoidales, etc., se ajustan intervalos al cabo de los cuales se genera el aviso de mantenimiento correspondiente. Los estados como Máquina des, Listo para arrancar, Servicio, Advertencia y Avería se encuentran también en la imagen de proceso.
Desde el punto de vista del cliente, decidirse por estas versátiles máquinas «plug & play» fue una cuestión fácil, previa presentación de una comparativa detallada con el gasto de conseguir las mismas funcionalidades por medio de la electroautomatización de componentes independientes. Estaba muy claro que no se conformaría con adquirir los distintos componentes, como las soplantes, el convertidor de frecuencia y los armarios eléctricos metálicos. La comparación detallada de las funcionalidades de las máquinas y de la regulación contemplaba también los costes de los relés de conmutación y disparadores de sobreintensidad para la conexión de accionamientos auxiliares, como ventiladores, bombas de aceite y de vacío, así como transformadores y unidades de evaluación para sensores de temperatura, presión y nivel o presión de aceite. Las señales registradas por los sensores deben valorarse y compararse con umbrales establecidos, y a partir de ahí, deberán implementarse acciones lógicas conmutadas eléctricamente. No había, como en otros casos, interfaces cuyo uso no estuviese claro, y la puesta en marcha pudo realizarse rápidamente y sin problemas. Además, todo está claramente documentado, con certificados CE y EMC, lo que también contribuye a la seguridad de servicio. La integralidad del suministro simplificó la planificación de los costes de inversión y también el cálculo comparativo de los costes de energía, ya que los datos de rendimiento de la máquina completa se presentaban de forma transparente desde el inicio.
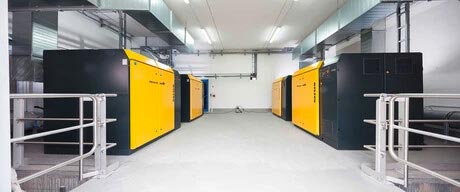
Aparte de la seguridad de planificación y legal, cabe también nombrar la seguridad de procesos. Si el control remoto fallara alguna vez, las soplantes pueden cambiarse a modo manual independientemente del sistema superior de control y con toda sencillez a través de los menús del SIGMA CONTROL 2, sin tener que modificar el cableado ni los parámetros (como pasaba antes con la conexion a convertidores de frecuencia externos, etc.). De este modo, las soplantes podrían ser en caso de emergencia las últimas máquinas que quedasen en funcionamiento y suministrar el aire necesario para mantener con vida los microorganismos de la fase de activación.
Resultado
Resumiendo los dos años de funcionamiento hasta ahora, el director del proyecto nos habla del buen servicio prestado por las cuatro modernas soplantes de tornillo y sus convertidores de frecuencia, por el controlador y la conexión a los puestos de mando. Y además, nos dice que los datos de rendimiento indicados para las soplantes responden realmente a los valores de garantía de la ISO 1217, anexo E, de manera que se consigue en la práctica la excelente eficiencia energética pronosticada en los documentos. El director de proyecto nos informa también de que ahorraron notablemente en la suma de inversión gracias a la integralidad de las máquinas.
Fotos fuente Kaeser Kompressoren