A menudo se puede lograr mucho con solo unas pocas medidas para aumentar la eficiencia y el ahorro de costos del suministro de aire comprimido.
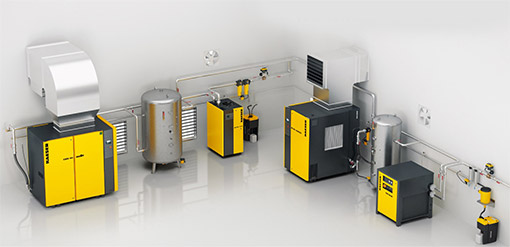
Se describe los puntos clave a observar en el proceso de renovación de un sistema existente o planificación de uno nuevo, y brinda algunos consejos sobre optimización.
Los costos de energía representan la mayor parte de los costos totales de suministro de aire comprimido. Para un suministro de aire comprimido optimizado producido por una nueva estación con compresores refrigerados por aire, el perfil de costos se divide de la siguiente manera: la puesta en servicio y la capacitación del personal de mantenimiento representan alrededor de solo el 1% de los costos totales; lo mismo ocurre con el tratamiento de condensados.
Los gastos de instalación y el costo de los controladores y los sistemas de control de procesos ascienden a siete, y la adquisición de equipos de tratamiento a cinco, mientras que el de los equipos compresores ronda el 13%. El mantenimiento de los compresores representa 3%, mientras que el mantenimiento del sistema de tratamiento representa el 1%. El bloque de costos más grande por un gran margen se deriva de los gastos de energía para suministrar compresores y equipos de tratamiento, sin embargo, al 69%. Esta sorprendente cifra deja en claro cómo el rendimiento energético es uno de los índices más importantes para evaluar compresores.
Realizar análisis de forma independiente
Se recomienda quien deseen planificar su propio sistema de aire comprimido que comiencen el análisis al final del sistema, es decir, con los consumidores, y trabajen paso a paso hacia atrás hasta la producción de aire comprimido en sí.
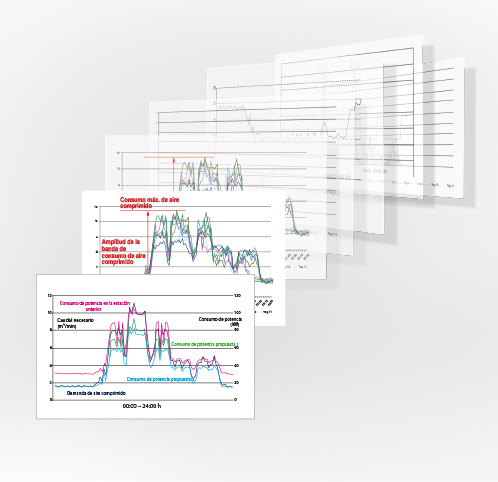
El primer aspecto a considerar es la calidad del aire comprimido y cómo se obtendrá.
Naturalmente, los niveles de calidad del aire comprimido requeridos por los consumidores dependen ante todo de las necesidades de cada empresa; los requisitos y clasificaciones relevantes se definen en ISO 8573 y proporciona recomendaciones de clase de pureza por tipo de aplicación. Los factores decisivos son determinar la calidad requerida por el consumidor, decidir cómo lograrla e identificar los posibles puntos débiles.
En algunos casos, especialmente para las empresas que han crecido orgánicamente con el tiempo, es posible que se estén realizando tratamientos innecesarios. Por ejemplo, esto se aplica cuando un usuario ha instalado recientemente un sistema de tratamiento con el único propósito de eliminar los contaminantes que han ingresado al aire comprimido debido a redes de aire comprimido sucias o materiales de tubería inadecuados, aunque la estación central de aire comprimido es capaz de suministrar la calidad del aire comprimido. Un tratamiento adicional significa una pérdida de presión adicional constante, costos de energía adicionales y mayores costos de mantenimiento.
La renovación de la red de aire comprimido puede ser una inversión sensata, especialmente si los puntos de consumo también requieren varias presiones diferentes y la infraestructura de distribución de la empresa es ineficaz. Por ejemplo, si el 80% de los consumidores funcionan a 6 bares y solo el 20% a 10 bares, toda la red debería funcionar a 10 bares, aunque esto es completamente innecesario. Cada bar adicional de presión en el sistema aumenta los costos de energía en aproximadamente un 7% sin ningún beneficio adicional. Cuanto mayor sea el potencial para reducir la presión del sistema, mayores serán los ahorros potenciales. Además, esta medida también reduce la caída de presión y las pérdidas por fugas. Por tanto, puede tener sentido instalar dos redes independientes.
Tuberías: material, conexión, accesorios
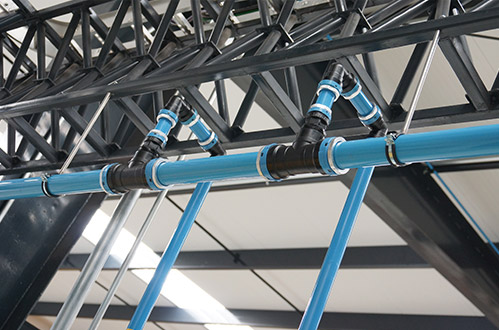
Las tuberías son el siguiente componente del sistema aguas arriba de los consumidores. Los criterios importantes aquí son: forma de colocación de la tubería, material, forma de distribución del aire comprimido en toda la empresa y método de unión de las tuberías entre sí y con los componentes.
El sistema de tuberías debe colocarse en tantas líneas rectas como sea posible para ahorrar energía. Las curvas, como las que rodean los pilares de soporte, se pueden evitar colocando la tubería en línea recta junto al obstáculo. Las esquinas pronunciadas de noventa grados causan una gran pérdida de presión y se pueden reemplazar fácilmente con curvas de 90 grados de generosas dimensiones. También se deben usar válvulas esféricas con paso completo, no reducido.
En la parte de la tubería aguas arriba del secador (lado húmedo), las entradas y salidas de la línea principal deben colocarse hacia arriba o al menos lateralmente. La tubería principal debe tener una pendiente del 0,2% y se debe proporcionar un medio de separación de condensado en el punto más bajo de esta línea. Por otro lado, las líneas se pueden colocar horizontalmente y las salidas de la tubería pueden conducir directamente hacia abajo en la parte seca de la tubería aguas abajo del secado.
La técnica de unión también es muy importante. Las piezas de la tubería deben conectarse entre sí mediante soldaduras, conexiones engarzadas para asegurarse de que tales uniones reducirán las posibles fugas al mínimo. Los sistemas de tubería sellados con cáñamo presentan un riesgo especialmente elevado de fugas, ya que la pasta de cáñamo se seca con el tiempo, lo que compromete la estanqueidad de las juntas de las tuberías. Este problema se agrava cuando se requiere aire comprimido muy seco. Por tanto, los sistemas de conductos sellados con cáñamo deben sustituirse.
Fugas
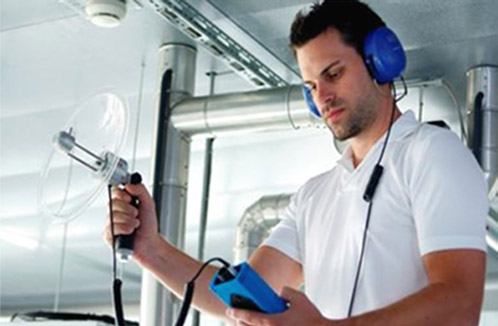
Las fugas en el sistema son las causas más activas de desperdicio de energía en una empresa, ya que trabajan las 24 horas del día, 8.760 horas al año; como era de esperar, por lo tanto, representan la fuente más importante de pérdidas en la mayoría de los sistemas.
Los estudios demuestran que entre el 25 y el 60% del aire comprimido producido se pierde debido a fugas, y las fugas ocurren con regularidad incluso en sistemas cuidadosamente mantenidos. Por lo tanto, siempre es un buen consejo prestar especial atención a la construcción de un sistema hermético y sin fugas.
Pero, ¿qué es un rango aceptable? Un valor de fuga de alrededor del 5% del volumen total se considera ahora como el nivel máximo dentro de la tolerancia; por el contrario, los valores del 10 por ciento o más requieren absolutamente una acción correctiva. Las fugas en el sistema hacen que aumenten los tiempos de funcionamiento del compresor y los costos operativos de energía, al tiempo que aumenta la frecuencia de los intervalos de mantenimiento.
Diámetro del orificio mm |
Consumo de aire a 6 bar(g) m3/min |
Pérdida kW |
Pérdida USD/año* |
1 | 0,065 | 0,46 | 604 |
2 | 0,257 | 1,80 | 2.364 |
4 | 1,03 | 7,21 | 9.474 |
6 | 2,31 | 16,17 | 21.247 |
* Costo de potencia eléctrica: 0,15 USD/kWh
Potencia específica asumida del compresor: 7kW/(m3/min)
Tratamiento y compresores
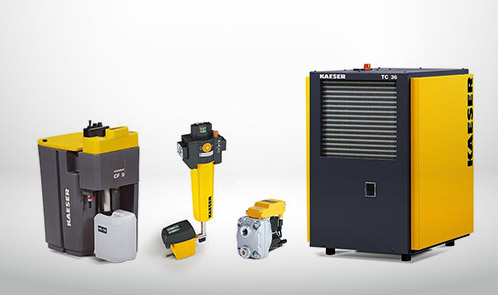
Una vez que el enfoque se ha desplazado a la propia estación de aire comprimido, el tratamiento de aire comprimido se convierte en la primera área a considerar. Los criterios clave incluyen el diseño de los secadores de aire comprimido, así como el estado de su tecnología. Los modelos más antiguos, como los secadores frigoríficos de derivación de gas caliente (HBPR= Hot By Pass Regulator), necesariamente funcionan de forma continua y no pueden cambiar al modo de espera cuando no se necesitan. Por el contrario, los secadores modernos que ahorran energía pueden hacerlo, lo que significa que consumen mucha menos energía. Además, es posible que la disposición de los secadores ya no refleje las condiciones reales si las temperaturas o las condiciones ambientales han cambiado, por ejemplo.
Sin embargo, la interacción entre los compresores puede tener un efecto definitivo sobre el consumo de energía si es ineficiente, como cuando los ajustes ya no coinciden con el perfil de demanda actual. ¿Los compresores cambian con frecuencia entre el funcionamiento en carga y en vacío? ¿El compresor de velocidad variable funciona constantemente en el rango de caudal superior o inferior? Estos son indicadores de que el sistema de aire comprimido existente no coincide con el perfil de consumo y/o la interacción entre los compresores (secuencia de uso) no está configurada de manera óptima. En sistemas con hasta dos compresores, un técnico puede configurar los ajustes correctos del controlador. Para sistemas más grandes con tres o más compresores, es recomendable consultar también a un experto técnico experimentado. En la mayoría de los casos, una configuración coordinada con precisión de compresores con diferentes capacidades resulta ser la solución ideal. Por lo general, consiste en máquinas de carga base y de reserva grandes, combinadas con máquinas de carga máxima más pequeñas.
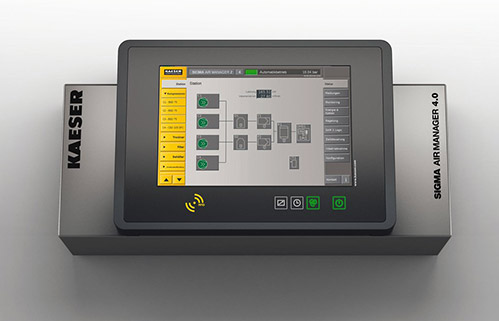
El controlador maestro es responsable de coordinar la producción del aire comprimido requerido con la máxima rentabilidad. Para hacerlo, debe tener la capacidad de cambiar automáticamente entre la combinación más favorable de compresores de carga base y de carga máxima en un momento dado, dentro de un rango de fluctuación de presión de solo 0,2 bar para hasta 16 compresores.
Los sistemas de control inteligentes pueden realizar esta hazaña altamente desafiante utilizando un sistema de bus para intercambiar datos con compresores y otros componentes, como drenajes de condensado, secadores, etc. Estos pueden luego conectarse a un sistema de control de proceso central al que todos los datos operativos se envían donde se pueden utilizar para la gestión avanzada de energía, por ejemplo.
Fotos fuente: Kaeser Kompressoren.