Eficiencia y Ecología juntas con el programa KAESER CARBÓN CERO
La nueva tecnología reduce los costos y ahorra espacio
El secado por refrigeración es el método de tratamiento más importante para el aire comprimido, aunque en el pasado era un proceso relativamente intensivo en energía, con perspectivas limitadas para la integración de opciones de ahorro de energía. Ahora, sin embargo, las nuevas y emocionantes tecnologías de masa térmica permiten ahorros significativos cuando se trata de proporcionar un secado por refrigeración efectivo de aire comprimido para sistemas de compresores que entregan hasta 34 m³/min y también permiten un diseño de unidad significativamente más compacto.
En condiciones normales, el aire ambiente contiene vapor de agua. La cantidad de vapor de agua que el aire es capaz de retener depende de la temperatura ambiente. Cuando la temperatura del aire aumenta, la capacidad del aire para absorber vapor de agua también aumenta. El grado en que el aire está saturado con agua se describe como “humedad relativa”. Si este aire ambiente normal es luego aspirado por un compresor y comprimido, la proporción de vapor de agua por unidad volumétrica de aire comprimido también aumenta. Si la temperatura del aire comprimido desciende, como suele ocurrir en el post enfriador del compresor, el aire comprimido se sobresatura, lo que hace que el exceso de agua se condense; esta agua se denomina “condensado”.
Más agua de lo esperado
A menudo se subestima la cantidad de condensado que sale del aire comprimido. Tomemos el ejemplo de un compresor en Alemania. Tiene un caudal de, digamos, 10 m³/min y una presión de trabajo de 9 bar, toma aire ambiente a una temperatura de 20 °C con un 60 por ciento de humedad, la cantidad de condensado resultante durante un período de 24 horas será total alrededor de 140 litros. Si la temperatura aumenta a un máximo de alrededor de 35 °C con un 30 por ciento de humedad, el volumen de condensado aumenta a 160 l por día. Sin embargo, para temperaturas predominantes similares en Asia, donde la humedad suele ser mucho más alta, alrededor del 80 por ciento, la cantidad resultante de condensado puede triplicar fácilmente esta cifra común para Alemania.
El compresor en sí solo comprime el aire ambiente. Si el aire comprimido no se trata adecuadamente aguas abajo del compresor, el condensado que contiene pasará sin obstáculos al sistema de aire comprimido.
El enfriamiento posterior del aire comprimido hasta la temperatura ambiente del sistema de aire comprimido provoca la acumulación continua de condensado adicional. Esto puede provocar la corrosión de las tuberías o incluso dañar la maquinaria de producción, sin mencionar los posibles efectos adversos en la calidad de los productos que se fabrican. Por todas estas razones importantes, es crucial eliminar la humedad directamente dentro de la propia estación de aire comprimido para evitar la formación de condensación en el sistema de aire comprimido aguas abajo y reducir la humedad relativa del aire comprimido hasta alrededor del 30 por ciento.
Hay disponible una variedad de métodos de secado para tratar el aire comprimido, cada uno de los cuales es más o menos adecuado, según los requisitos del proceso de producción específico en cuestión. De los muchos métodos de secado disponibles, el secado por refrigeración es el más común, ya que ofrece suficiente rendimiento y calidad de aire comprimido para la mayoría de los usos. Los valores instantáneos son decisivos y representan hasta el 20 por ciento de la energía total requerida para la producción de aire comprimido.
Afortunadamente, los secadores frigoríficos se han beneficiado de las innovaciones técnicas a lo largo de los años. Hasta principios de la década de 1990, los secadores frigoríficos eficientes presentaban un intercambiador de calor aire/aire, en el que primero el aire comprimido frío saliente enfriaba el aire comprimido entrante, creando así una especie de sistema de recuperación de energía. Al mismo tiempo, el consiguiente proceso de recalentamiento sirvió para reducir la humedad relativa del aire comprimido saliente por debajo del 30 por ciento y evitó la acumulación de condensado en el exterior de las tuberías que transportan el aire comprimido más frío. Después de pasar por una fase de enfriamiento previo en el intercambiador de calor aire/aire, un intercambiador de calor aire/refrigerante enfrió el aire comprimido hasta 3°C en la mayoría de los casos.
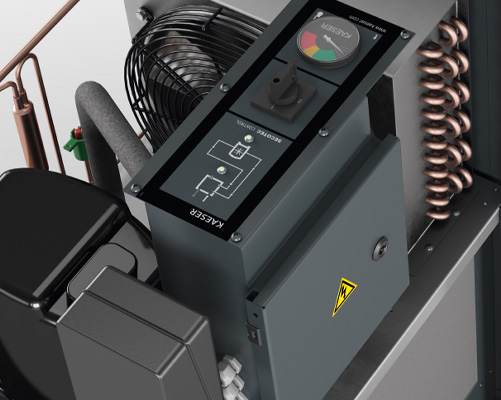
El circuito de refrigerante a menudo estaba equipado con un “control de derivación de gas caliente”, que desviaba el refrigerante de regreso al circuito cuando se requería menos enfriamiento como resultado del bajo consumo de aire. Este sistema resultó en una pérdida de energía en diversos grados ya que el compresor de refrigerante siempre estaba funcionando básicamente a la misma salida (para hacer circular el circuito de refrigerante). La única forma de reducir un poco la carga en el secador frigorífico cuando el compresor funcionaba a capacidad parcial era apagar el ventilador de refrigeración; Sin embargo, esto solo arrojó resultados menores, ya que este ventilador del condensador consumía relativamente poca energía en comparación con el sistema en su conjunto.
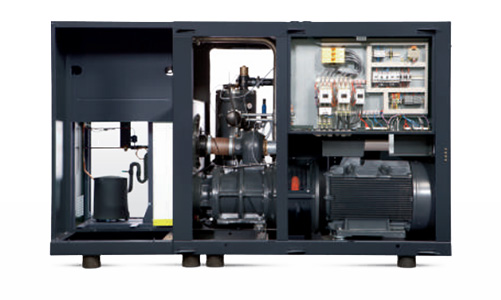
Para sistemas grandes, es decir, aquellos con un caudal superior a 50 m³/min, se conoce desde hace algún tiempo un método para ajustar el rendimiento del secador frigorífico para que coincida con la demanda real durante los períodos de menor consumo de aire comprimido. Esto se logró utilizando compresores de refrigerante con múltiples cilindros, que se apagaron individualmente según correspondiera durante la operación de carga parcial. Esta sigue siendo una opción eficaz hoy en día para obtener un rendimiento eficiente de estos secadores frigoríficos a gran escala durante el funcionamiento de carga parcial.
Medidas de optimización energética
A mediados de la década de 1990 se desarrollaron tres métodos diferentes para mejorar el rendimiento de los secadores frigoríficos que funcionan con caudales de aire inferiores a 50 m³/min en carga parcial:
• Compresores de gas refrigerante “Scroll digital”
• Compresores de gas refrigerante de velocidad variable
• Secadores frigoríficos de masa térmica
El método scroll digital implicaba modificar las pérdidas de espacio libre dentro del compresor scroll utilizado para el refrigerante, que a su vez regulaba el caudal de refrigerante para ajustarlo a la cantidad requerida para enfriar el aire comprimido. La ventaja de este método era que permitía un rango de control relativamente grande; sin embargo, la dificultad técnica de implementarlo lo hizo menos atractivo. Además, además de un compresor scroll para cubrir la carga base, este método también empleaba un compresor scroll controlado que se apagaba completamente durante los períodos de muy baja demanda.
En términos de compresores con control de velocidad variable, una desventaja era que solo era posible regular el compresor de refrigerante dentro de un rango relativamente pequeño; entonces fue necesario hacer la transición nuevamente al control de derivación de gas caliente. Por lo tanto, este sistema fue capaz de ahorrar solo una pequeña cantidad de energía durante la operación de carga parcial.
La masa térmica en los secadores frigoríficos ofrece mayores ahorros
Los secadores intermedios fueron la tecnología preferida para caudales de aire comprimido inferiores a 20 m³/min. Algunos sistemas dependían de un tanque, similar a la forma en que funciona un receptor de aire comprimido dentro de un sistema de aire comprimido, para amortiguar las fluctuaciones de carga mientras se mantiene la presión relativamente constante y se reduce al mínimo la conmutación del compresor. Esto significa que cuanto más grande sea el tanque, menores serán las fluctuaciones de presión y, por lo tanto, se requerirán menos cambios. Otros sistemas se basaban en una masa térmica, que absorbe la energía térmica, en lugar de incorporar un tanque de compensación de aire frío. Estos secadores generalmente usan materiales minerales para almacenar la energía de enfriamiento. Para mantener la frecuencia de conmutación del compresor de refrigerante dentro de los límites económicos y garantizar un punto de rocío constante, la cantidad de masa necesaria aumenta en proporción directa a la capacidad del sistema. Además, la distribución del calor dentro de la masa térmica requiere una regulación precisa.
Factor limitante: el peso excesivo del equipo
Las consideraciones de peso imponen ciertas restricciones de tamaño en estos tipos de secadores de aire comprimido, aunque el sistema de masa térmica en sí mismo es esencialmente ideal. No implica cargas mecánicas ni maniobras de ningún tipo de sistema, ya que solo es necesario encender y apagar el secador frigorífico según sea necesario en función de la producción de aire comprimido, y su funcionamiento es extremadamente confiable.
Además, cuando la masa térmica está saturada, el sistema mantiene reservas de seguridad para adaptarse a periodos de sobrecarga de corta duración. Sin embargo, los secadores de masa térmica adecuados para capacidades de aire comprimido relativamente modestas de 17 a 20 m³/min son extremadamente pesados, con un peso de unos 850 kilos. Hasta hace poco, los sistemas más grandes tenían que estar equipados con sistemas de desplazamiento digital y no podían beneficiarse de las ventajas de los secadores de masa térmica.
Fotos fuente: KAESER Kompressoren.