Tiempo estimado de lectura: 7:40 min
Eficiencia y Ecología juntas con el programa KAESER CARBÓN CERO
Observemos las causas para entender y controlar los costos operativos de un sistema de aire comprimido.
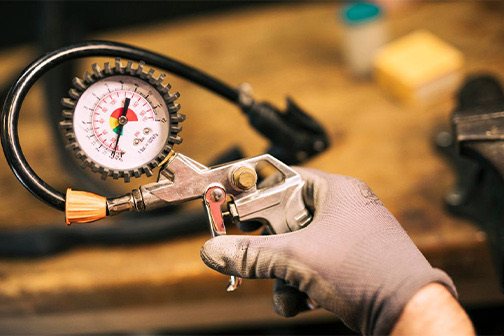
Los compresores de desplazamiento positivo impulsan aire, no crean la presión. El sistema neumático crea la contrapresión frente a la que los compresores deben generar. Si el compresor suministra más aire del que requiere la demanda, la presión aumentará y en el caso contrario desciende cuando existe un defecto de suministro de aire comprimido.
Cuando una aplicación neumática exige que la presión sea mayor de la necesaria, se crea un gasto de energía en el sistema. Este gasto energético no es lineal con el aumento de la presión, podría ser exponencial por diferentes situaciones, siendo las principales la demanda artificial y la mayor capacidad volumétrica de los compresores en el sistema.
De acuerdo a las mediciones realizadas en las auditorías de aire comprimido, el 25 al 30% de la potencia energética en la mayoría de los sistemas de aire comprimido se debe a un incorrecto seteo de presión alta del sistema.
Si identificamos los consumos que están generando una mayor presión, podemos reducir el consumo energético de los compresores de aire.
Otro punto a tener presente es que las demandas productivas siempre superan cualquier ajuste de control de los compresores. Es importante comunicar que la demanda de aire no será sensible la presión del sistema, de esta manera se convierte al sistema más confiable y eficiente energéticamente beneficiando la calidad y la productividad.
Identificar la ineficiencia

La manera más sencilla de determinar qué consumos están impulsando la presión del sistema es preguntar a los técnicos operativos de la sala de compresores cuales son las más sensibles a las variaciones de presión que suelen recibir una comunicación si una boca de consumo de aire comprimido no funciona correctamente para identificar la misma. Generalmente esas comunicaciones generan un ajuste mayor en la presión operativa de los compresores hasta que la demanda funciona de manera normal. Esta es una corrección que no tiene en cuenta el proceso para solucionar lo que puede haber causado. En su lugar, compensa todos los problemas con el aumento de la presión del sistema.
Si un filtro está obstruido o se produce una fuga en el punto crítico de uso, requerirá una presión más alta para todo el sistema para proporcionar la misma presión operativa. Por lo tanto, la presión requerida está determinada por la sumatoria de los diferenciales de presión del sistema sumado a la presión real requerida en las bocas de consumo.
Diagrama de un perfil de presión de un sistema de aire comprimido
El diagrama muestra un perfil de presión de un sistema de aire comprimido desde la generación hasta el consumo y es característico en la mayoría de los sistemas de aire comprimido que se auditan. Cuando se presenta el perfil de presión de esta forma, es más fácil determinar dónde se encuentran las mayores pérdidas de presión y cómo mejorar el rendimiento del sistema.
Mejorar la eficiencia
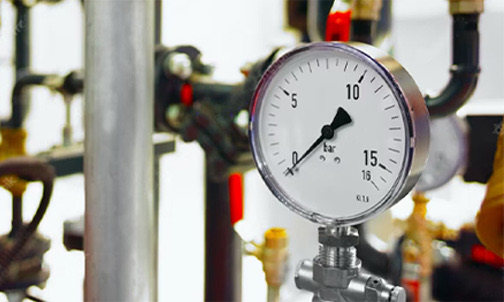
Hay dos formas de aumentar la presión en el artículo sobre el consumo de aire comprimido. Podemos aumentar la presión del sistema o disminuir las pérdidas de presión entre los compresores y la presión del consumo. Aumentar la presión del sistema es la solución más fácil pero más cara en términos de costos operativos.
Resulta que la mayoría de las empresas no hacen un seguimiento del costo del aire comprimido, los costos adicionales se pierden en el presupuesto general y no están asociados con la decisión de aumentar la presión.
La regla general es que cada aumento de un bar en la presión de los sistemas aumenta la potencia requerida del compresor en línea en un 7%.
Como ejemplo, en un sistema de compresores de 200 kW de potencia nominal instalada, aumentamos la presión en 1 bar para superar un problema productivo, se obtendría un aumento del 7% o 14 kW de potencia eléctrica de consumo, pero esta consecuencia es solamente una parte del análisis. El aumento de la presión aumenta la demanda de aire por parte de todos los usuarios que no están ajustados, incluidas las fugas, el soplado directo de aire comprimido y las bocas de consumo con el regulador completamente abierto y es la llamada demanda artificial. En un sistema de 200 kW, la demanda artificial representará fácilmente 2 m³/min adicionales de demanda u otros 14 kW debido al aumento de la presión. Si este aumento de la demanda requiere que se encienda un compresor adicional, el aumento de la potencia será desproporcionado. Si el compresor de respaldo tuviera 132 kW, la potencia en líneas de aire posiblemente aumentaría en 66 kW o más.
La estrategia es analizar las pérdidas de presión y reducir las pérdidas entre los compresores y la presión en las bocas de consumo de producción. En el diagrama de presión del sistema, hay más de 2 bar de pérdida de presión desde la presión de base hasta la presión confiable al producto. Una parte de esta pérdida es atribuible a una capacidad volumétrica inadecuada (desconocer los reales consumos de aire). Analizaremos la otra causa que es la pérdida de presión creada por los componentes del punto de uso: el filtro, el regulador, el lubricador (llamado FRL) y las mangueras de interconexión.
Localizar la caída de presión
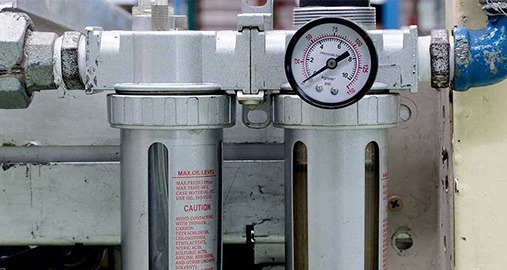
Podría ser difícil medir la caída de presión en un consumo intermitente con manómetros. Es recomendable tener un manómetro de presión delta P de precisión. La observación de la medición da un conocimiento de la presión delta en un consumo puntua. La diferencia entre el punto de ajuste del regulador FRL cuando es estático y la presión estable cuando el consumo está circulando se aproximará a la pérdida de presión.
Como regla general, los resultados del análisis son que los componentes del punto de uso (el filtro, el regulador, el lubricador y las mangueras) son los lugares para reducir fácil y significativamente las pérdidas de presión.
En el perfil del diagrama, la pérdida de presión debido a estos componentes se muestra como 1 bar (6,2 a 5,2 barg), pero a menudo es tan alta como 1,7 a 2 bar. Esta es una verdadera pérdida de fricción debido a la resistencia al caudal, por lo tanto, depende de la presión, la temperatura y la velocidad de caudal en el uso. Pero estos componentes normalmente están dimensionados para que coincida con el tamaño de la tubería de conexión y no se seleccionan en función de la pérdida de presión aceptable. A una presión de 6,2 barg y caudal de 1,1 m³/min, una unidad de mantenimiento FRL estándar de conexión 1/2″ causa 1,2 bar de pérdida de presión.
En una aplicación neumática que es mandatario la presión operativa del sistema, se justifican componentes de mayor calidad están disponibles en el mismo tamaño nominal de conexión con deltas P de diseño más bajos, también los componentes estándar pueden ser de gran tamaño en uno o dos tamaños nominales para lograr un resultado similar (el sobredimensionamiento de la unidad FRL podría aumentar la histéresis, lo que puede producir en problemas en las aplicaciones críticas o intermitentes del consumo). Se recomienda diseñar una pérdida total de presión en el punto de uso menor a 0,4 bar de diferencial, que permita que la carga de suciedad de la unidad de mantenimiento FRL del filtro aumente el delta P hasta un 0,6 bar. Es fundamental recordar que este análisis debe basarse en el caudal operativo, no en el consumo promedio.
El caudal operativo es el volumen requerido en un período de tiempo específico corregido a estándar metro cubico por minuto. Por ejemplo, si un punto de conexión utiliza 0,1 m³/min estándar en seis segundos una vez por minuto, el consumo promedio sería de 0,1 m³/min estándar y uno podría instalar incorrectamente componentes de 1/2” esperando una pérdida de presión mínima. Pero el caudal operativo real se calcula:
0,1 m³/min x 60 segundos / 6 segundos = 1 m³/min y generará la pérdida de presión menor a 1,2 bar expuesta anteriormente.
Para obtener el caudal operativo de un fabricante de equipos neumáticos, uno debe hacer preguntas muy específicas porque siempre mencionarán la tasa media de consumo, no el caudal operativo más alto en un momento específico.
La reducción de las pérdidas de presión que uno identifica permite una presión de funcionamiento más razonable, y las reducciones resultantes en la potencia del compresor en línea pueden ser sorprendentes. Pero, debido a que el almacenamiento en un sistema de aire comprimido es una función del tamaño físico de los tanques más la tubería y el diferencial de presión útil que está disponible, la reducción de la presión del sistema disminuye la capacidad de almacenamiento.
Este es un problema relativamente sencillo, abordar el mal rendimiento del consumo requiere un esfuerzo adicional y menos costoso de solucionar.
Conclusiones
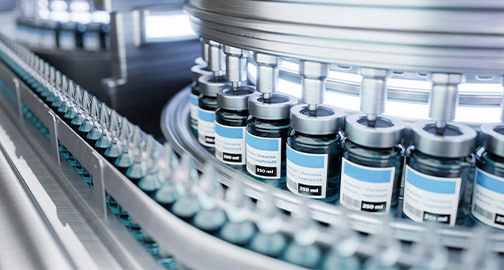
En la mayoría de los usuarios de aire comprimido, algunos de estos problemas de punto de uso establecen la presión de funcionamiento de todo el sistema. Concentrándose en el consumo que requiere presión más alta y en aquel consumo con problemas de rendimiento, uno asimilará rápidamente cuál deber ser la presión de base práctica más baja y eficiente para el sistema.
La mejora en el rendimiento de los consumos es en forma individual, beneficioso y captará el apoyo del personal de producción.
Fuente de información:
Dean E. Smith, iZ Systems
Compressed air BEST PRACTICES
Fotos fuente: Kaeser Kompressoren