Tiempo estimado de lectura: 00 min
Este es un ejemplo de aplicación en el uso de la válvula de carga principal de aire KAESER DHS para equilibrar el caudal entre dos sistemas de aire comprimido separados.
Generalidades
Muchas empresas operan con una sola estación de aire comprimido de forma centralizada abasteciendo a todos los puntos de consumo, pero es usual encontrar con múltiples sistemas de aire dentro de las plantas. En empresas productivas muy grandes con varias naves, esta solución que a continuación detallamos podría ser la forma más económica de aplicar, especialmente en zonas con climas fríos que requerieren secadores disecantes y probablemente en red de tuberías con sistemas de calefacción no utilizados en todos los sectores de planta.
Aquí abordaremos el caso de aplicación de la válvula DHS en el que se emplean sistemas de aire separados para garantizar la presión y calidad del aire específica por separado, que en muchas oportunidades se elige utilizar sistemas independientes de generación y tratamiento con fines de seguridad. Generalmente en estos casos los usuarios conectan los sistemas con una válvula manual y la abren según sea necesario, pero esto es obviamente un inconveniente y no se puede regular bien. La automatización de esta función evitará complicaciones en las operaciones.
Ejemplo de aplicación
A continuación, detallamos cómo un cliente nos consultó con el problema: Dos sistemas de aire comprimido que operaban a diferentes presiones y niveles de calidad del aire.
Una empresa de mantenimiento de aeronaves utiliza dos compresores de tornillo rotativos lubricado KAESER modelo BSD de 37 kW para el aire del taller principal para llevar a cabo sus operaciones, revisando una amplia variedad de aviones comerciales y militares. A posterior añadieron un nuevo sistema de prueba que utilizó grandes volúmenes de aire comprimido durante períodos cortos para simular las condiciones de vuelo. Para esto compraron un sistema completo de tratamiento en aire seco y limpio con dos compresores de tornillo rotativos lubricado KAESER modelo DSD de 110 kW cada uno, secador refrigerativo, filtros, tanque pulmón de 15 m3, etc. (con planes futuros para un tercer compresor). Este sistema incluía un controlador maestro Sigma Air Manager (SAM 4.0) para el control y la supervisión remota.
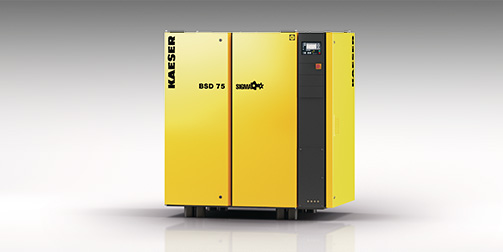
Compresor de tornillo rotativo lubricado KAESER BSD de 37 kW
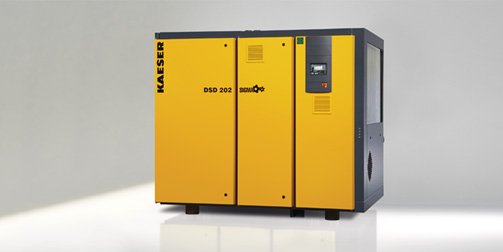
Compresor de tornillo rotativo lubricado KAESER DSD de 110 kW
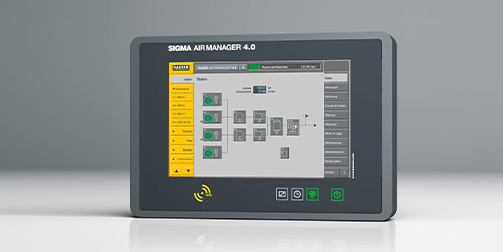
Controlador maestro Sigma Air Manager (SAM 4.0)
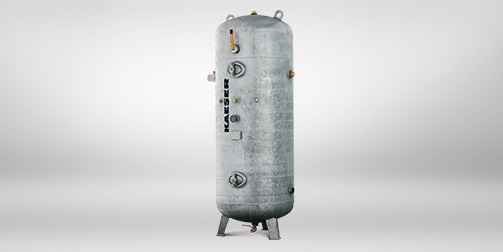
Tanque pulmón
Tenían la intención de operar estos sistemas por separado la mayor parte del tiempo, pero a veces el sistema BSD se quedaba sin aire y necesitaba volumen adicional.
El cliente quería conectar los dos sistemas para que el sistema más grande pudiera aumentar el sistema más pequeño cuando fuera posible, alimentando el aire de los compresores KAESER DSD en la aplicación de prueba a los compresores KAESER BSD sobrecargados de trabajo en el sistema de aire del taller. El sistema de aire de prueba tenía una mayor calidad del aire y era importante evitar que el aire del taller de menor calidad contaminara el aire del sistema de prueba. Esencialmente, el cliente quería que el aire circulara de la aplicación de prueba a la aplicación de aire del taller cuando fuera necesario, pero bajo ninguna circunstancia el aire de la ubicación del taller podía entrar en el sistema de aplicación de prueba.
Nuestra solución inicial fue conectar las dos redes de tuberías y conectar los cuatro compresores al controlador maestro SAM 4.0 y ejecutar todos a la misma presión operativa. El desafío era que el sistema dedicado a la aplicación de prueba requería una presión operativa más alta (8 barg) que el sistema dedicado al aire de taller (7 barg), y el cliente no quería aumentar la presión en el sistema de aire del taller (habría desperdiciado una energía considerable, cada bar de aumento 7% de energía eléctrica). Además, la aplicación de prueba consume un gran volumen de aire en un corto período de tiempo, y también consumiera simultáneamente el aire necesario para el taller cuando se estaban realizando las pruebas. En resumen, querían que el sistema de aplicación de prueba alimentara el sistema de aire de la tienda de vez en cuando, pero no querían que la aplicación de prueba robara aire del sistema de la tienda durante los períodos de prueba de alto volumen de consumo.
Este caso en particular requería una solución algo creativa, y se logró con una válvula de carga principal de aire KAESER DHS.
Por lo general, estas válvulas se instalan para garantizar la calidad del aire en un sistema de aire comprimido, detectando la presión del aire aguas arriba de la válvula y cerrándola si la presión aguas arriba cae por debajo del umbral establecido (lo que causaría caudales de mayor velocidad que impedirían el tiempo de contacto adecuado en el tratamiento, por ejemplo, secadores frigoríficos). Esta lógica también funciona bien para esta aplicación cuando la válvula está instalada con su sensor de presión ubicado en el lado “protegido” de la válvula.
En el caso, eso significa instalar la válvula DHS con su sensor de presión en el lado del aire del taller para garantizar que la presión en el sistema de aire de la tienda nunca bajara por debajo de 7 barg, y nunca se vería afectada cuando la aplicación de prueba se está operando en el otro sistema. La mayoría de las veces, se permite que el sistema de prueba suministre aire al taller, pero durante el período de prueba (un evento de alta demanda de consumo de aire), es posible que la presión del sistema de prueba caiga por debajo de la presión de aire del taller. En estos momentos, la válvula de carga principal de aire Kaeser DHS se compromete a evitar la pérdida de presión para los usuarios de aire del taller y para garantizar que el aire de menor calidad del taller no contamine los instrumentos de prueba más sensibles en el otro sector.
La válvula de carga principal de aire KAESER DHS tenía un punto de ajuste de 7,2 barg, por lo que, si la presión en el sistema de prueba caía por debajo de 7,2 barg, cerraría y aislaría los dos sistemas, evitando así efectivamente que la presión cayera demasiado baja en el taller. Una vez que la presión se elevara por encima del punto de ajuste de 7,2 barg en el sistema de aire del taller, válvula de carga principal de aire KAESER DHS volvería a abrir y ambos sistemas volverían a ser comunes, lo que permitiría que el aire de los compresores KAESER modelos DSD complementara al taller nuevamente.
Tener presente que se recomendó una válvula de retención para evitar que el aire de menor calidad del taller contamine el aire de mayor calidad de la aplicación de prueba.
Si bien la aplicación de ensayos de prueba generalmente se ejecuta a una presión más alta que la del taller, ocasionalmente puede caer por debajo durante eventos de alta demanda, por lo que la válvula de retención garantiza que no haya contaminación en el lado de la prueba.
Para más obtener más información, por favor visite nuestro sitio web de KAESER Compresores de Argentina
INGRESAR AHORA
Fuente: Grayson Atkinson, Director de diseño de sistemas, KAESER USA.
Fotos fuente: Kaeser Kompressoren.