Tiempo estimado de lectura: 5:30 min
Sistema de recuperación de calor en compresores de tornillo refrigerados por aceite
El calor del aceite refrigerante se transfiere al sistema de agua caliente mediante el intercambiador de calor adjunto al compresor. La cantidad de calor transferido es la cantidad que reduce la temperatura del aceite a la temperatura óptima de funcionamiento a plena carga. Un sensor de temperatura y un control del caudal de agua garantizan que la temperatura del agua se mantenga prácticamente constante (p. ej., 55°C). Si el requerimiento de agua caliente se reduce, el aceite se envía automáticamente al enfriador combinado enfriado por aire (instalado como estándar).
El calor residual del enfriador se puede canalizar para calentar un espacio cerrado.
Si es requerido temperaturas de salida de agua más altas de hasta 70°C, se recomienda otros intercambiadores de calor, como intercambiadores de calor de casco y tubos, intercambiadores de calor de placas de fácil mantenimiento.
Sistema de recuperación de calor en compresores enfriados por aire o por agua
El agua caliente para diversos fines puede generarse a partir de un compresor refrigerado por aire o agua por medio de un intercambiador de calor instalado en el circuito de aceite de enfriamiento. El intercambiador de calor puede ser un tipo de placa simple o, en casos específicos, un intercambiador de casco y tubos.
Figura 1: Sistema interno de recuperación de calor en compresor a tornillos lubricado.
Posibilidades de controlar la recuperación de calor
Los compresores a tornillos lubricados tienen un contacto libre de voltaje o “contacto seco” con la señal de “motor en marcha”, esta señal se puede utilizar para controlar una bomba o una válvula solenoide de cierre en el circuito de recuperación de calor para controlar el caudal de agua.
En los compresores KAESER con SIGMA Control 2 tiene la posibilidad de programar un valor umbral de la temperatura de salida de la unidad compresora medida en una salida. Esto solo permite la utilización de la recuperación de calor cuando el compresor ha alcanzado una determinada temperatura de trabajo. Este se recomienda para compresores con baja utilización y también para compresores controlados por frecuencia.
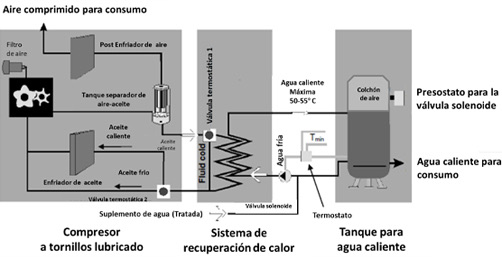
Figura 2: Sistema de recuperación de calor de agua caliente en compresor a tornillos lubricado.
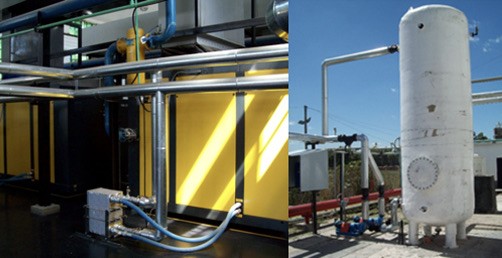
Figura 3: Imagen del sistema de recuperación de calor en compresor a tornillos lubricado.
Instalación de intercambiador de calor fuera del compresor
• El intercambiador de calor debe instalarse cerca del compresor.
• Debe montarse con un pie o un marco equipado en el suelo.
• No debe instalarse a un nivel superior a los puertos de entrada y salida de aceite en el compresor.
• Si el intercambiador de calor se instala por encima del nivel de aceite interno, el aceite adicional del intercambiador de calor fluirá hacia el tanque del separador de aceite y puede provocar un golpe de ariete en el sistema. También puede ocasionar un daño en la unidad de compresión debido a que, en el próximo arranque, el intercambiador de calor de aceite se llena primero y durante este tiempo no lubricará ni enfriará el bloque compresor.
Figura 4: Instalación de intercambiador de calor fuera del compresor.
Ahorros de calentamiento de espacios con recuperador de calor
El aire de salida que transporta el calor del enfriador de aceite y de aire, instalado en un compresor a tornillos lubricado, es dirigido hacia un espacio cerrado próximo (por ejemplo, un depósito). Esta fuente de calor releva la carga en el sistema de calefacción del área, recuperando así el aceite caliente del compresor.
Ejemplo 1 de cálculo: Cálculo de ahorro por recuperación de calor del aceite de compresor a tornillos lubricado de 45 kW
Potencia del motor: 48,3 kW
Eficiencia del motor: 0,96
Período de calentamiento: 125 días
Período de carga: 8 horas x día
Precio por calentar aceite: 0,70 USD / litro
Calor específico del aceite: 35,5 MJ / litro = 9,87 kWh / litro
Relación: (1 MJ = 0,278 kWh)
Eficiencia de calentamiento: 0,9
Consumo total de potencia eléctrica: 51,4 kW
Energía utilizable en aire caliente
Phrs= 96% del consumo de potencia total
0,96 x 51,4 kW = 49,3 kW
Ahorro de energía recuperable del aceiteEnergía utilizable x tiempo carga x precio aceite
Calor específico aceite x eficiencia calentamiento
49,3 kW x 1.000 h x USD 0,70 / l
9,87 kWh / l x 0,9
Ahorro USD 3.888 a 1.000 hs en carga máxima por año
Ejemplo 2 de demanda de energía térmica: Compresor a tornillos lubricado enfriado por aire para calentamiento para un espacio cerrado de 300 m²
El cálculo se basa en una demanda anual promedio de energía de calefacción de 150 kWh / (m²/a), según un estudio energético realizado por el gobierno alemán. Como regla, este valor depende del tipo de edificio, su antigüedad y el aislamiento. Con respecto a este ejemplo, los requisitos anuales de calefacción de un espacio cerrado de 300 m² pueden ser suministrados por el calor recuperado de un compresor de tornillo único con una potencia nominal de 45 kW. Sin embargo, debe entenderse que el tiempo de funcionamiento del compresor y, por lo tanto, el calor disponible, dependen de la demanda de aire comprimido.
El cálculo anterior utiliza un compresor a tornillos lubricado como sistema de carga base continua. Siempre permitir un margen de seguridad, para tener en cuenta los diferentes modos de operación, la carga y los diferentes consumos de energía de los compresores a diferentes presiones finales de aire y aire (por ejemplo, optimización del sistema por reducción de presión).
Potencia Nominal: 45 kW
Potencia del motor: 48,3 kW
Eficiencia del motor: 0,96
Consumo anual de energía de acuerdo al actual consumo: 150 kWh / (m² / año)
Período de calefacción: 125 días
Período de carga del compresor: 8 horas por día
Consumo total de energía al año
300 m² x 150 kWh / (m²/año) = 45.000 kWh / año
Demanda de calentamiento x día: 45.000 kWh / año
Energía utilizable de la salida del compresor (aire caliente): 49 kW
Energía de calentamiento utilizable por día:
49 kW x 8 hora / día = 392 kWh / día
Ejemplo 3 de cálculo del ahorro de calentamiento agua para gas natural
Potencia nominal motor accionamiento compresor: 18,5 kW = 25 HP
Rendimiento térmico máximo disponible motor: 15,2 kW
Poder calorífico por m³ de gas: 10,2 kW-h / m³
Grado de rendimiento de la calefacción por gas: 1,05
Precio por m³ de gas: 0,75 USD / m³
Consumo anual: 2.000 hs / año
Ahorro de costos:
2.129 USD al año
Calculo de la cantidad de energía aprovechable en forma de calor
Para más información consultar en:
Fotos fuente: Kaeser Kompressoren.