Tiempo estimado de lectura: 4:45 min
Eficiencia y Ecología juntas con el programa KAESER CARBÓN CERO
La Abfall-Verwertungs-Gesellschaft mbH de Hamburgo forma parte del grupo Indaver, y ha sido una de las primeras empresas que se ha especializado en la incineración controlada de residuos especiales e industriales a alta temperatura, realizando una labor pionera en la eliminación de residuos industriales como la primera planta incineradora de este tipo en Alemania, en funcionamiento desde 1971. Hasta el día de hoy, sus estándares de calidad y protección del medio ambiente sirven como referencia en su rama.
La incineración a alta temperatura es la actividad principal de la eficiente Abfall-Verwertungsgesellschaft mbH de Hamburgo. Desde unas obras de renovación realizadas en los años 90, esta planta incineradora de residuos especiales se cuenta entre las más grandes y modernas de su clase del mundo. Actualmente puede eliminar hasta 159.000 toneladas de residuos al año. El calor generado en la combustión se transfiere a la red de calefacción urbana de Hamburgo por medio de una planta de cogeneración cercana. De este modo, el calor de la incineradora sirve para calentar hasta 30.000 hogares.
Energía ganada a partir de residuos
La incineración a alta temperatura es un proceso meticulosamente controlado que lleva asociada una compleja limpieza de los gases de escape acorde a los estándares más modernos. La incineradora funciona ininterrumpidamente, en turnos de 24 horas, 7 días a la semana. Está formada por dos líneas de incineración idénticas e independientes entre sí que se someten a control y a mantenimiento alternativamente. Cada una de esas líneas cuenta con su propio sistema de limpieza final de los gases de escape. Las condiciones óptimas para la incineración y el sistema de limpieza de gases de alta eficacia reducen las emisiones de la planta al mínimo posible, manteniéndolas no solo por debajo de los valores límite de la Ley alemana de control de emisiones, sino también claramente por debajo de los requisitos de la oficina de licencias de Hamburgo, que son más exigentes.
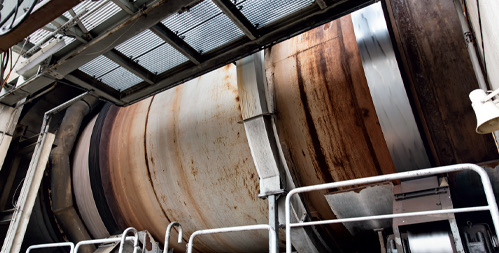
El componente principal de cada línea de incineración es un horno rotativo de doce metros de longitud.
El componente principal de cada una de las líneas es un horno rotativo de doce metros de longitud que gira lentamente alrededor de su eje para revolver los residuos y garantizar así su combustión completa. Mientras que la escoria va enfriándose en agua, los gases pasan a la cámara de postcombustión, donde se destruyen los posibles compuestos orgánicos residuales, como pueden ser dioxinas y furanos. Es en la caldera de recuperación donde los gases derivan la mayor parte de su calor para la generación de vapor caliente, con el que después se alimenta la red de calefacción urbana. Luego, un filtro eléctrico elimina el polvo del gas una vez enfriado. Los metales pesados, el cloruro de hidrógeno y el dióxido sulfúrico se eliminan posteriormente en varias fases húmedas de purificación.
Renovar lo viejo
En la planta incineradora, el aire comprimido sirve, entre otras cosas, para transportar los residuos por medio de bombas neumáticas de diafragma y para extraer la ceniza pulverizada de la caldera y del filtro eléctrico. Además, contribuye a la pulverización de los residuos dentro del horno y en la cámara de postcombustión, desempeñando un papel importante en la hermetización de seguridad de la planta, que dejaría de funcionar si la presión descendiera por debajo de 3,8 bar. Thomas Pöthe (director del Dpto. de producción) lo resume así:
“Si nos faltase el aire comprimido, aunque solo fuera temporalmente, no podríamos mantener en marcha la incineración y la planta se detendría. Por eso, la confiabilidad absoluta del aire comprimido es indispensable para nosotros.”Thomas Pöthe (director del Dpto. de producción)

Estación de aspiración con bombas neumáticas de diafragma.
La antigua estación, parcialmente reformada en 1997 y luego en 2014, ya no cumplía esta condición. “Teníamos problemas con la cobertura de la demanda cuando había que realizar trabajos de mantenimiento, y con la ampliación gradual de la planta, los dos compresores viejos de 160 kW llegaron también a su límite de suministro”, nos dice Lars Schubert, responsable de mantenimiento y gestión de recursos. Cuando se instalaron más bombas neumáticas de diafragma en el año 2018 por la construcción del nuevo almacén de combustible y volvió a subir el consumo de aire comprimido, quedó claro que era el momento de renovar la estación de compresores. Las condiciones de la autoridad competente incluyen la utilización de “la mejor técnica disponible” (BVT en sus siglas alemanas), de modo que la AVG Hamburg se puso en contacto con el servicio exterior de KAESER.
El análisis con ADA (Air Demand Analysis) dio como resultado que se necesitaba un caudal equivalente a tres veces 30 m3/min a una presión aproximada de 7,0 bar. Pero la nueva estación debía diseñarse de manera que no se limitase a cubrir esa demanda de forma confiable, sino que además debía ofrecer margen para ampliaciones posteriores. La nueva estación de aire comprimido KAESER se puso en marcha en 2021. Con el fin de crearle también un espacio óptimo se construyó incluso una nave nueva. Actualmente, cuatro compresores de tornillo DSDX 305 (pres. de servicio máx. 8,5 bar) suministran el aire comprimido necesario con seguridad, dos secadores refrigerativos de bajo consumo HYBRITEC DTI 668-902 se ocupan del tratamiento del aire proveniente de los compresores nuevos y de los viejos que siguen en servicio.
Todo el sistema es monitorizado y regulado por un controlador maestro SIGMA AIR MANAGER 4.0. Como la confiabilidad del sistema es de una importancia vital, Thomas Pöthe y Lars Schubert tienen en gran consideración el factor mantenimiento, y nos resumen satisfechos:
“Estamos muy contentos con el alto estándar técnico de la estación, el buen asesoramiento que hemos recibido de KAESER y con la confiabilidad de su servicio de asistencia.”Thomas Pöthe (director del Dpto. de producción)
Fotos fuente: KAESER Kompressoren